CNC Precision Machining Suppliers: Elevate Your Manufacturing Processes
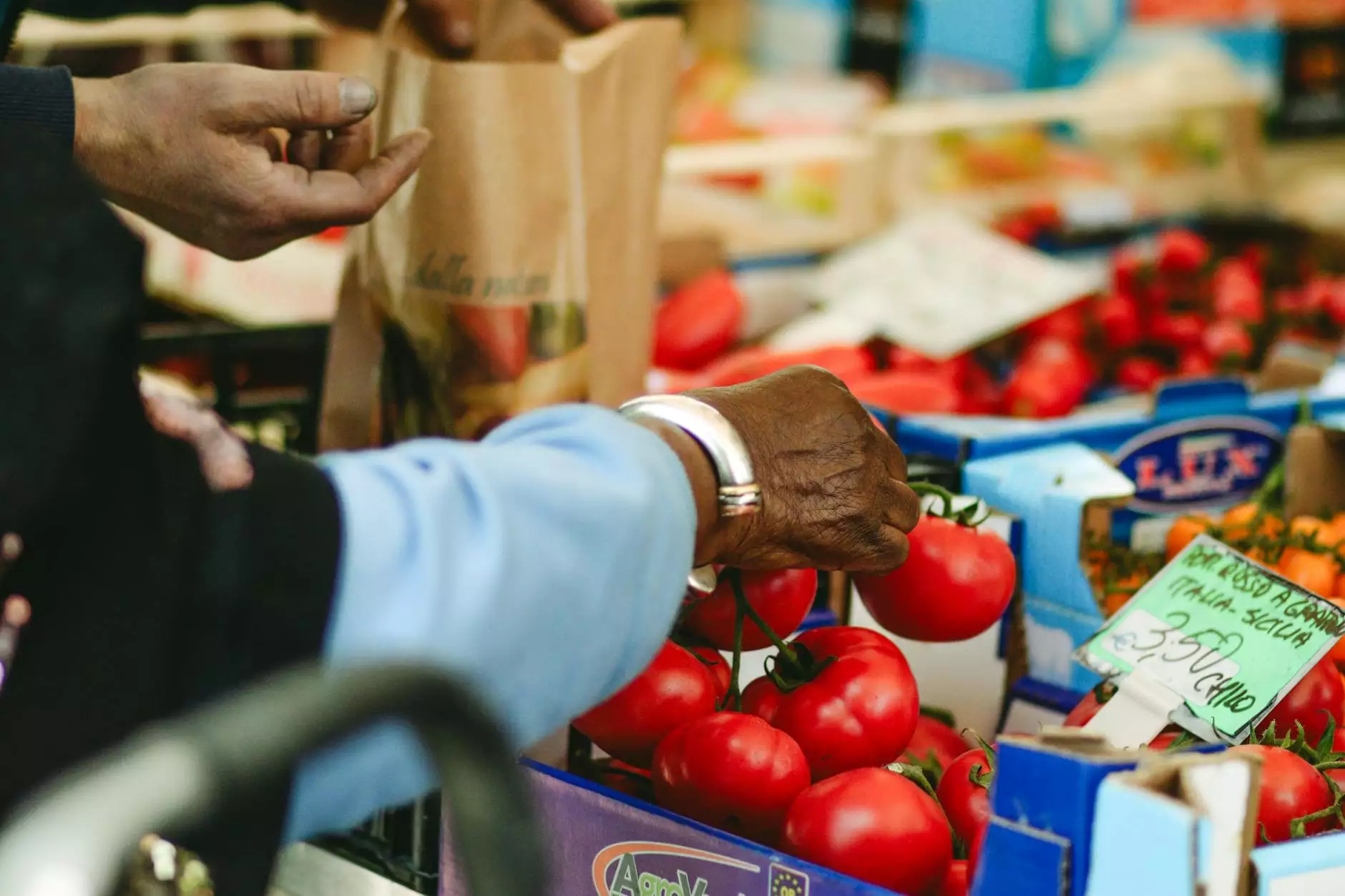
In today's cutting-edge manufacturing landscape, CNC precision machining suppliers play a pivotal role in providing high-precision components essential for various industries. From aerospace to automotive, the demand for meticulously crafted parts is skyrocketing. As businesses strive to enhance their production efficiency, understanding the significance of partnering with a reliable CNC precision machining supplier becomes paramount.
Understanding CNC Precision Machining
CNC (Computer Numerical Control) precision machining is a manufacturing process that utilizes computer-controlled tools and machinery to create intricate and high-quality parts. This advanced technology allows for unparalleled accuracy, consistency, and repeatability in manufacturing processes. CNC machining can produce a wide variety of parts made from different materials, including metals, plastics, and composites.
The Importance of Precision in Manufacturing
Precision is crucial in manufacturing due to several reasons:
- High Tolerance Levels: CNC machining offers the ability to maintain extremely high tolerance levels, ensuring parts fit together perfectly.
- Enhanced Efficiency: The automated nature of CNC machines allows for faster production times, reducing lead times for projects.
- Cost-Effectiveness: While the initial investment may be higher, the reduced waste and need for rework contribute to lower overall costs in the long run.
- Versatility: CNC machines can handle various tasks, including milling, turning, drilling, and grinding, making them suitable for multiple applications.
Choosing the Right CNC Precision Machining Supplier
Selecting an appropriate CNC precision machining supplier is critical to ensuring the success of your manufacturing projects. Here are key factors to consider when evaluating potential suppliers:
1. Experience and Expertise
Look for suppliers with a proven track record in the industry. A supplier with years of experience is more likely to possess the technical expertise needed to meet your specific requirements.
2. Quality Assurance
Ensure that the supplier implements stringent quality control measures. Certifications such as ISO 9001 can be indicators of a supplier's commitment to quality and consistent output.
3. Range of Services Offered
Different suppliers may specialize in various types of machining, such as turning, milling, or electrical discharge machining (EDM). Assessing the range of services offered will help determine whether a supplier can cater to your unique needs.
4. Pricing and Value
While cost should not be the sole determining factor, it is essential to find a supplier who offers competitive pricing without compromising on quality. Request quotes from multiple suppliers to make an informed decision.
5. Customer Support
Excellent customer support is vital in maintaining a productive relationship with your supplier. A responsive supplier who provides timely communication and support can significantly ease the project management process.
Benefits of Partnering with a CNC Precision Machining Supplier
Collaborating with a reputable CNC precision machining supplier can yield numerous benefits for your business:
1. Access to Advanced Technology
CNC precision machining suppliers invest in cutting-edge technology and equipment, allowing you to benefit from the latest advancements in machining without making significant investments in new machinery.
2. Technical Expertise
Suppliers often have skilled machinists and engineers who can provide valuable insights into design optimization and material selection, ensuring the best possible outcome for your projects.
3. Scalability
As your business grows, your production needs may evolve. Partnering with a CNC precision machining supplier allows you to scale your production capacity without the challenges of purchasing new equipment or hiring additional staff.
4. Risk Mitigation
Working with an established CNC machining supplier reduces the risks associated with manufacturing defects, leading to higher customer satisfaction and a better market reputation.
Applications of CNC Precision Machining
CNC precision machining serves a wide array of industries. Here are some notable sectors where precision machining is indispensable:
- Aerospace: The aerospace industry requires components that meet rigorous safety and performance standards. CNC machining is used to create lightweight, yet strong parts such as turbine blades and structural components.
- Automotive: In automotive manufacturing, CNC precision machining is essential for producing intricate parts with high tolerances, such as engine blocks and transmission components.
- Medical: The medical industry relies on CNC machining for manufacturing surgical instruments, implants, and devices where precision is paramount to ensure patient safety.
- Electronics: CNC machining is also used to manufacture enclosures, brackets, and other components critical to electronic devices.
Quality Control in CNC Precision Machining
Quality assurance is at the heart of CNC precision machining. The following practices are crucial to ensuring high-quality outputs:
1. In-Process Inspection
During the machining process, regular inspections can help catch defects early, minimizing waste and rework.
2. Final Product Testing
Once the machining process is complete, conducting tests on the finished products is essential to ensure they meet all specified requirements and tolerances.
3. Continuous Improvement
A good CNC precision machining supplier will engage in continuous improvement practices, regularly reviewing processes and implementing changes based on feedback and performance metrics.
Case Study: Success Through CNC Precision Machining
Let’s consider a hypothetical example of a company in the automotive sector seeking to improve the production of a high-performance engine component. By partnering with a seasoned CNC precision machining supplier, the company achieved the following:
- Improved Production Speed: By leveraging advanced CNC machinery, the supplier reduced production time by 25%.
- Enhanced Part Quality: With stringent quality control measures, the rate of defective parts dropped significantly from 10% to just 1%.
- Cost Savings: Overall, the combined efforts of quality and efficiency led to a reduction in production costs, allowing the company to reinvest into innovation.
Conclusion: The Future of CNC Precision Machining Suppliers
The role of CNC precision machining suppliers is more critical than ever in a world that demands precision and rapid production. By collaborating with a skilled supplier like Deep Mould, businesses can harness the power of advanced manufacturing technologies. As we move into the future, continued advancements in CNC machining technology will undoubtedly lead to new possibilities, reshaping industries and enhancing efficiency across the board.
In conclusion, when choosing a CNC precision machining supplier, it is essential to focus on experience, quality assurance practices, and the range of services provided. The right partnership can significantly elevate your production capabilities and help you remain competitive in today's ever-evolving market.