Understanding the Role of Plastic Injection Mold Manufacturers
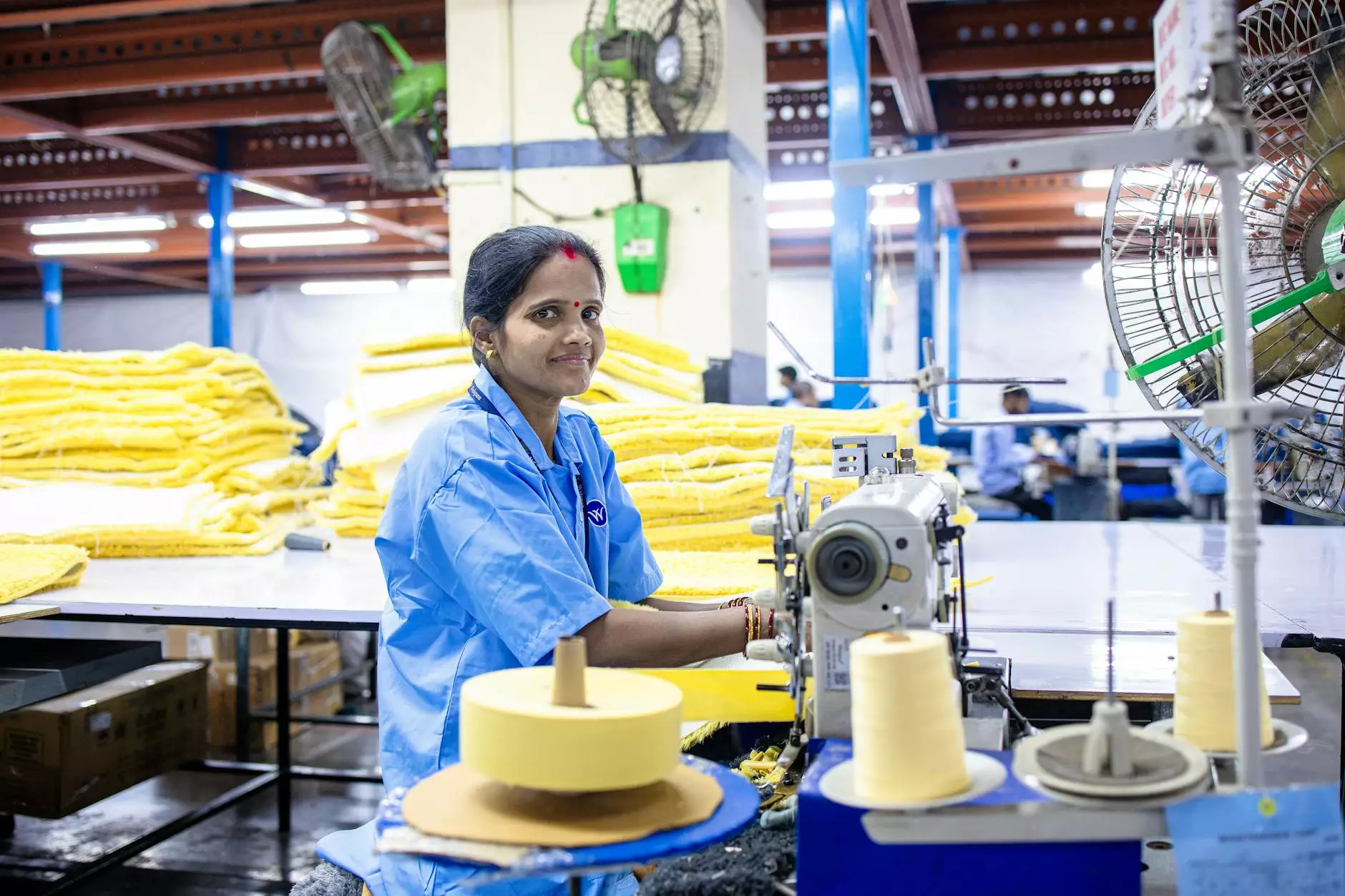
Plastic injection mold manufacturers play a vital role in the modern manufacturing landscape. They are responsible for creating high-quality molds that are essential for producing plastic parts in a wide array of industries such as automotive, electronics, consumer goods, and healthcare. With advancements in manufacturing technologies and techniques, these manufacturers not only ensure the functionality of plastic components but also contribute to product design, efficiency, and sustainability.
The Basics of Plastic Injection Molding
At its core, plastic injection molding is a manufacturing process in which molten plastic is injected into a mold cavity to create a desired shape. This method is favored for its ability to produce high volumes of components quickly and with great precision. Here’s how the process works:
- Material Selection: The first step involves selecting the appropriate plastic resin, which may vary in terms of strength, flexibility, and durability.
- Heating: The chosen resin is heated until it reaches a molten state, making it easier to mold.
- Injection: The molten plastic is then injected into a pre-designed mold.
- Cooling: Once the mold is filled, the plastic cools and solidifies, taking the shape of the mold.
- Demolding: Finally, the newly formed plastic part is ejected from the mold.
Importance of Quality in Manufacturing
Quality assurance is paramount in the realm of plastic injection mold manufacturing. High-quality molds ensure that the final products meet the specified standards of strength, dimensional accuracy, and surface finish. Here are some key factors that plastic injection mold manufacturers must focus on to maintain quality:
- Material Quality: The choice of materials used in mold-making significantly affects durability and performance.
- Precision Engineering: Advanced machining techniques and cutting-edge technology help in achieving exact specifications.
- Testing and Validation: Rigorous testing processes ensure that molds perform reliably under operational conditions.
Innovation and Technology in Plastic Injection Molding
As technology evolves, so do the methods employed by plastic injection mold manufacturers. Innovations such as automation, artificial intelligence, and advanced CAD software are revolutionizing the industry:
- Automation: Robotic systems enhance efficiency by managing repetitive tasks, thus reducing human error and fatigue.
- 3D Printing: Prototyping with 3D printing allows manufacturers to test designs quickly and affordably before committing to final production.
- Simulation Software: This software enables manufacturers to predict potential issues and optimize designs before physical production.
Sustainability in Plastic Injection Molding
With growing awareness of environmental concerns, sustainability has become a significant focus for plastic injection mold manufacturers. They are increasingly adopting eco-friendly practices:
- Recyclable Materials: Using biodegradable and recyclable materials helps reduce waste.
- Energy Efficiency: Implementing energy-efficient processes minimizes the carbon footprint associated with manufacturing.
- Waste Reduction: Techniques such as optimizing cycle times and utilizing regrind materials contribute to reducing waste.
Choosing the Right Plastic Injection Mold Manufacturer
Selecting the right plastic injection mold manufacturer is crucial for ensuring quality and efficiency in the production process. Here are some tips to consider:
- Experience and Reputation: Research the manufacturer’s background, including years of experience and customer reviews.
- Technical Expertise: Assess their capabilities in handling complex molds and diverse materials.
- Production Capacity: Ensure they can meet your volume requirements and timelines.
- Customer Support: Evaluate the level of support they offer throughout the design and manufacturing process.
Future Trends in Plastic Injection Mold Manufacturing
As industries continue to evolve, plastic injection mold manufacturers must stay ahead of emerging trends. Some future trends include:
- Smart Manufacturing: The integration of IoT technology for real-time data monitoring and predictive maintenance is on the rise.
- Customized Solutions: Manufacturers will increasingly offer tailored solutions to meet specific client needs.
- Industry 4.0 Initiatives: Embracing digital transformation will help manufacturers streamline processes and improve overall efficiency.
Conclusion
As we dive deeper into the realm of plastic injection mold manufacturers, it becomes clear that their role is indispensable in producing the plastic components that are foundational to countless products across various industries. The commitment to innovation, quality assurance, and sustainability sets these manufacturers apart in a competitive market. With the continual evolution of technologies and manufacturing practices, the future of plastic injection molding promises exciting developments that will enhance the efficiency and effectiveness of the manufacturing process.
For businesses seeking reliable and proficient manufacturers, exploring partnerships with established leaders in plastic injection molding can significantly impact product quality and market competitiveness. DeepMould.net exemplifies the quality and expertise required in today’s demanding manufacturing landscape, ensuring that businesses receive the highest quality products that meet both their needs and those of their customers.